Innovations in Testing of Plastics: Improving Product Performance
In an era where plastic materials are integral to industries such as automotive, electronics, packaging, and healthcare, ensuring that plastics meet the highest standards of quality, durability, and sustainability is paramount. As technology advances, so do the methods for testing plastics. The introduction of innovative testing techniques has significantly improved product performance, reduced failure rates, and enhanced safety across various sectors.
This blog will explore the latest innovations in plastic testing and how they contribute to improving product performance by providing manufacturers with more accurate, efficient, and reliable data on plastic materials.
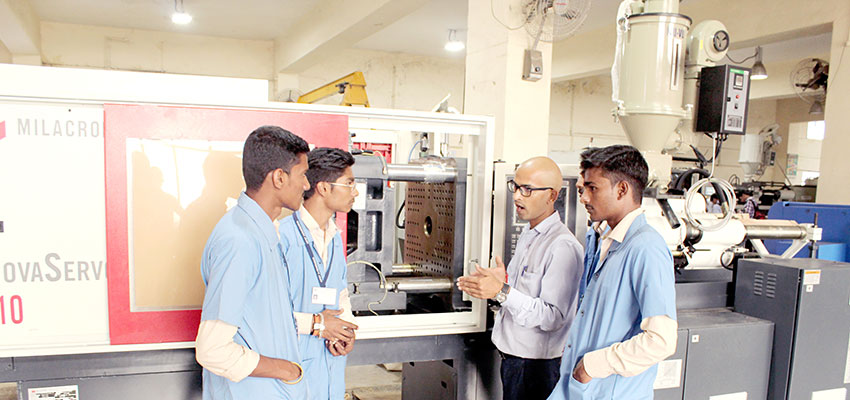
The Growing Importance of Plastic Testing in Manufacturing
Plastics have transformed industries due to their versatility, cost-effectiveness, and ability to be molded into complex shapes. However, the increasing demand for stronger, lighter, and more sustainable plastic materials has placed greater emphasis on the need for advanced testing methods. Testing ensures that plastics meet the stringent performance and safety standards required for their specific applications.
Why Traditional Testing Methods Are No Longer Enough
While conventional testing methods such as tensile strength and impact resistance remain crucial, they often provide only a limited snapshot of a material’s performance. With the development of more complex plastics and applications, manufacturers now require testing methods that can assess a wider range of material properties, including chemical resistance, environmental impact, and long-term durability.
Key Innovations in Testing of Plastics
In response to the evolving needs of industries, new and more sophisticated testing techniques have emerged. These innovations not only provide a deeper understanding of material properties but also enhance the speed and accuracy of testing, leading to better product development and performance.
1. Non-Destructive Testing (NDT)
One of the most significant innovations in plastic testing is Non-Destructive Testing (NDT). Unlike traditional methods that may require cutting or altering the sample, NDT allows for the inspection of plastic materials without causing any damage. This is particularly valuable in industries like aerospace and automotive, where product integrity is crucial.
Advantages of Non-Destructive Testing
- Preserves Material Integrity: NDT allows testing of a product without compromising its structure, making it ideal for expensive or highly specialized components.
- Early Defect Detection: This method helps identify internal defects, such as voids, cracks, or inclusions, before they lead to product failure.
- Increased Accuracy: By using techniques such as ultrasonic testing, X-ray, or infrared thermography, NDT provides highly accurate results, ensuring better quality control.
2. Automated Testing Systems
As manufacturing processes become more automated, automated testing systems are becoming essential for plastic testing. These systems use robotics and advanced software to conduct multiple tests simultaneously, significantly increasing testing efficiency and consistency.
Benefits of Automated Testing in Plastics
- Faster Testing Cycles: Automated systems can conduct tests rapidly, reducing the time required for product development and market introduction.
- Consistency and Accuracy: By removing human error, automated systems ensure more consistent and reliable test results.
- Data Integration: Automated testing systems often include data analytics capabilities, providing manufacturers with real-time insights into material performance and enabling faster decision-making.
3. Advanced Thermal Analysis Techniques
Plastic materials are frequently exposed to extreme temperatures, making thermal analysis a critical aspect of plastic testing. Traditional thermal testing methods such as Heat Deflection Temperature (HDT) are now being supplemented by more advanced techniques like Differential Scanning Calorimetry (DSC) and Thermomechanical Analysis (TMA).
Differential Scanning Calorimetry (DSC)
DSC measures the heat flow associated with material transitions, such as melting and crystallization. This technique provides critical data on a plastic's thermal stability, allowing manufacturers to design materials that perform well under high-temperature conditions.
Thermomechanical Analysis (TMA)
TMA assesses the dimensional changes in plastics when exposed to temperature variations. This method is essential for industries such as electronics and construction, where thermal expansion and contraction can lead to product failure if not properly accounted for.
4. Rheological Testing
Rheological testing measures the flow and deformation behavior of plastics under stress, which is crucial for processing and performance optimization. Innovations in this area, such as rotational rheometers and capillary rheometry, allow for more precise control over material properties, improving manufacturing processes and end-product quality.
Key Applications of Rheological Testing
- Injection Molding: Rheological data helps optimize the injection molding process, reducing defects such as warping or incomplete filling.
- Extrusion: In extrusion processes, understanding the flow characteristics of plastics ensures consistent production quality and minimizes waste.
5. Environmental and Sustainability Testing
As environmental concerns grow, the need for sustainable plastics has become a priority for manufacturers. Innovative environmental testing methods now assess how plastics degrade in natural environments and their overall environmental footprint. These tests are crucial for ensuring compliance with regulations like REACH and RoHS, which focus on reducing hazardous substances and promoting sustainability.
Biodegradability Testing
New testing methods can now accurately measure the rate at which biodegradable plastics break down in different environmental conditions. This is vital for ensuring that these materials do not contribute to long-term pollution.
Microplastics Testing
As concerns over microplastics in oceans and ecosystems rise, advanced testing methods are being developed to detect and measure microplastic particles in products and environments. These tests ensure that plastics used in packaging and consumer goods minimize their environmental impact.
Enhancing Product Performance through Advanced Plastic Testing
Innovative testing methods not only help manufacturers comply with regulatory standards but also play a significant role in improving product performance. By providing more accurate data on material properties, these advanced techniques enable manufacturers to design better, more durable, and more sustainable products.
Improving Durability and Strength
New testing methods such as fracture mechanics and fatigue testing offer insights into how plastics behave under repeated stress and prolonged use. This is particularly important for products used in automotive, aerospace, and construction industries, where materials are subjected to extreme forces over time.
- Fatigue Testing: Measures the endurance of plastic materials under cyclic loading conditions, helping to predict product lifespan and prevent premature failure.
- Fracture Mechanics Testing: Evaluates how cracks propagate in plastic materials, providing manufacturers with data to improve toughness and prevent catastrophic failures.
Enhancing Thermal and Chemical Resistance
Advanced testing methods allow manufacturers to select materials that can withstand harsh conditions, such as high temperatures or exposure to chemicals. This is crucial for industries like electronics, where materials must remain stable in extreme conditions.
- Thermal Gravimetric Analysis (TGA): Assesses how materials decompose at elevated temperatures, allowing manufacturers to select plastics with higher thermal stability.
- Chemical Resistance Testing: New methods now offer better insights into how plastics react with various chemicals, ensuring that materials remain durable and safe in environments with high chemical exposure.
Promoting Sustainability and Eco-Friendly Products
By incorporating advanced sustainability testing methods, manufacturers can develop plastics that are not only high-performing but also environmentally responsible. This is becoming increasingly important as consumers and regulators demand more eco-friendly products.
- Life Cycle Assessment (LCA): This innovative tool evaluates the environmental impact of a plastic material throughout its entire life cycle, from raw material extraction to end-of-life disposal. LCA helps manufacturers make informed decisions about material selection and product design.
The Future of Plastic Testing: What to Expect
As industries continue to evolve, the demand for more advanced and innovative plastic testing methods will only grow. The future of plastic testing will likely see the integration of artificial intelligence (AI) and machine learning, which can predict material performance and optimize testing processes in real time.
AI-Driven Testing Systems
AI has the potential to revolutionize plastic testing by analyzing vast amounts of data from previous tests to predict material behavior more accurately. This would allow manufacturers to simulate testing scenarios and make adjustments to material formulations before physical testing even begins.
Real-Time Monitoring and Smart Testing
Innovations in real-time monitoring technology could enable manufacturers to continuously test and monitor material properties during the production process. This would ensure that any variations in material quality are detected immediately, reducing the risk of defects and improving overall product performance.
Conclusion: Innovations Driving Plastic Testing Forward
As manufacturers face increasing pressure to improve product performance and sustainability, innovative plastic testing methods are becoming indispensable tools for ensuring quality, reliability, and compliance. By embracing the latest advancements in testing technologies, manufacturers can not only meet regulatory and performance requirements but also push the boundaries of what plastic materials can achieve.
The future of plastic testing is bright, with new technologies enabling faster, more accurate, and more comprehensive evaluations of material properties. By staying ahead of these innovations, manufacturers can ensure that their products remain competitive and meet the ever-evolving demands of the global market.